Common operational pain points overshadowed by external pressures
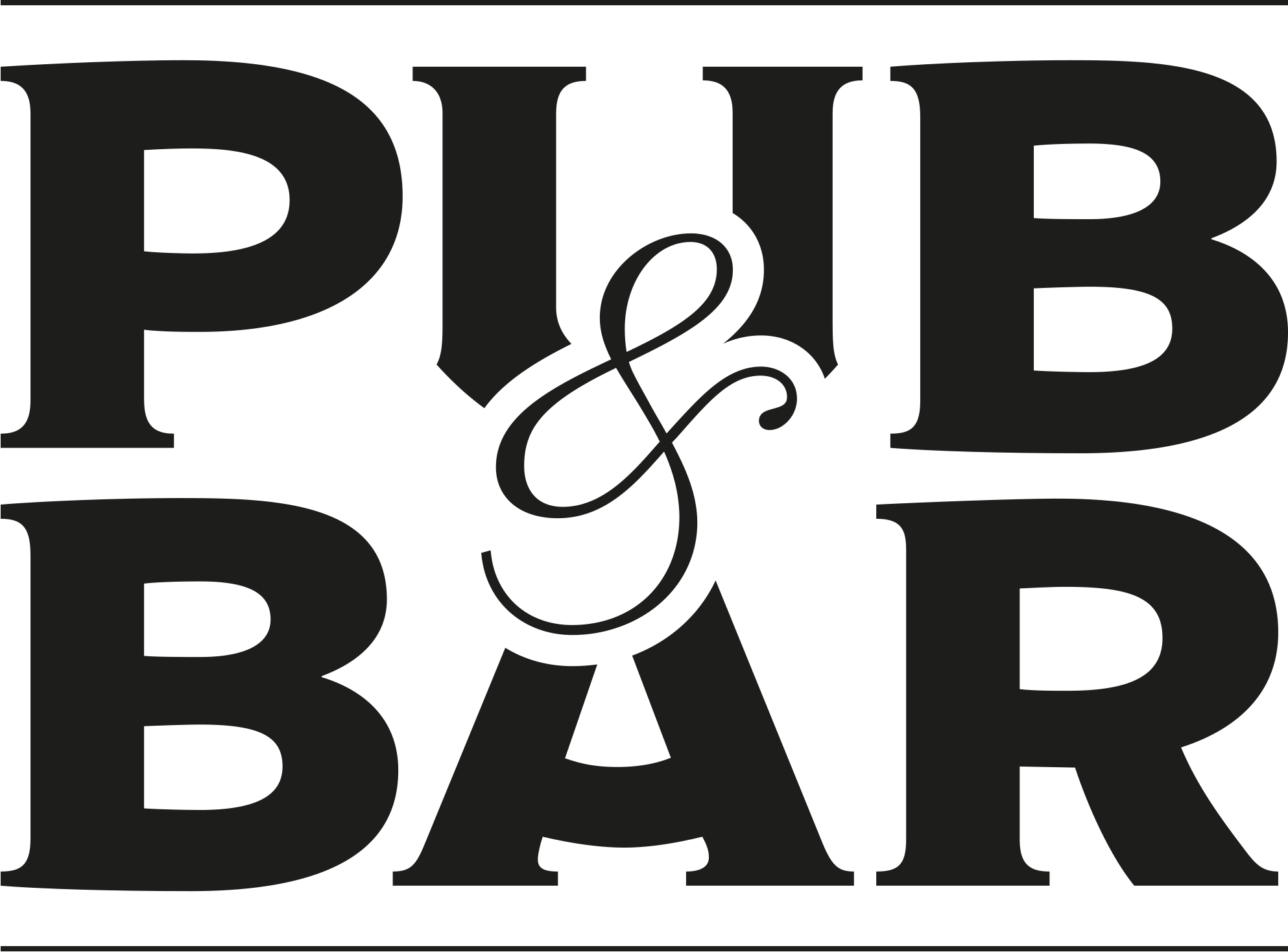
Cumulative rises in duties, increasing taxes and mounting business costs are taking over the general narrative of managing hospitality operations. Businesses facing these consistent roadblocks to generating profit are frequently unaware that their operational excellence is being eroded under the radar. According to Venners, daily nationwide retail losses could equate to millions of pounds across the industry due to common pain points.
Improper till usage
Manipulation of revenue reporting and intentional and improper usage of tills can be traced back to frequent unexpected error corrections, no sales or refunds. In depth analysis of sales and till data often exposes concerns with particular staff members, transactions or products.
Poor currency and stock security
Unlimited access to stock and moneys through basic procedure failures, such as stock in unsecure areas, keys not being locked up, absence of access record traceability and accountability, are some of the common operational faux pas.
Lax ordering, delivery and stocktaking practices
Issues with best practice inventory methods are on the rise. Overstocking and understocking, deliveries not being checked against original orders, unaccompanied delivery personnel, and inaccurate levels of stock or stock movement records, are some of the main culprits.
Slipping service standards
According to Venners Consultants, 38% of all retail loss is due to server errors. Performance reviews most commonly trace this back to the lack of training or due care of employees. This includes overpouring, wastage and spillage of stock, breakages of crockery and equipment.
Cost cutting instead of cost management
Although cost cutting is vital in times of external pressures, it can inadvertently damage the overall cost management strategy when done in isolation. Business critical activities such as detailed menu engineering and supplier cost price reviews are key to forecasting achievable results.
Policy and equipment maintenance
Not having time to enforce or regularly review policies in accordance with a business’ current situation stifles operational management. Equipment policies for usage and maintenance are one of the most common areas neglected in times of pressure.
Small steps of progression allow businesses to combat internal pain points effectively. Operational excellence coaching offers targeted advice on specific revenue and stock control related pain points.